Smart Plant Modernization of Core Process Control - Part 1
A lot has been said in the past 10 years about adding automation to plants for digital transformation of manual work. But the automation for the core process control (CPC) should also be modernized to require less manual intervention by production operators, for the plant to be more autonomous, to reduce instrument maintenance work, and to make the plant more sustainable.
Many old-style automation components remain in plants today because when they fail there is no time to review newer and better solutions, so they are replaced with identical components. Thus, there are still many mechanical instruments in operation. Those components were the best of their kind when originally selected, but today better solutions are available. Plants that do not keep automation up to date will be at a huge disadvantage in the long term. Instrumentation and controls problems have direct business impact. Modernizing automation help plants attain operational excellence. New plants being built now can use these technologies right from the start.
The core process control zone includes the distributed control system (DCS) and safety instrumented system (SIS), together referred to as the integrated control and safety system (ICSS), as well as the associated sensors and valves. These systems have rigorous management of change (MoC) procedures to preserve the robustness and safety of production. This article is about the automation in this CPC zone. But the CPC zone does play a part in digital transformation. Plants that successfully pursue digital transformation adopt the NAMUR open architecture (NOA) whereby data from the DCS is channeled securely through data diodes out to an independent monitoring and optimization (M+O) zone with automation for digital transformation of other functions. The data diodes make sure the security and robustness of the systems in the CPC zone are not affected. Open standard OPC-UA interfaces are used to make the DCS data available to the automation in the M+O zone. Thanks to this security, sensors and software apps can be added freely in the M+O zone.
Reducing manual intervention: Production
Instrumentation issues like failure, underperformance, inaccuracy, and lack of integration force production operators to manually intervene in loops that otherwise would be in automatic. Additional work causes stress, but various new, intelligent field instrumentation, controllers, and software components are available to help.
Transmitters with moving mechanical parts are susceptible to wear and failure, and when they do fail, production operators are forced to operate loops in manual. This, in turn, causes off-spec product, higher energy consumption, and operator stress, which may lead to mistakes. For example, displacer type interface level transmitters have moving parts. The recommendation is to upgrade these positions with guided wave radar (GWR) level and interface transmitters that have no moving parts whenever conditions permit.
Another mechanical example is turbine and positive displacement (PD) flowmeters. The recommendation is to upgrade these positions with magnetic, vortex, or Coriolis flowmeters with no moving parts. As a result of more reliable instruments, loops stay in automatic for greater sustainability and reduced off-spec product, plus operator stress is reduced. In addition, many new instruments now support Bluetooth wireless communication that enables configuration, calibration, and diagnostics at the device using a phone, tablet, or laptop.
When the process cycles or deviates from setpoint, it could be due to control valve issues like high friction or high/low air supply pressure. Or the problem could be elsewhere in the loop. When analog control valve positioners or I/P converters are used, production operators cannot tell there is a valve issue because there is no diagnostics or position feedback. So, production operators put the troubled loop in manual. Again, they will experience the same manual challenges described previously.
The recommendation is to upgrade all control valves with smart valve positioners with valve performance analytics. Valve issues can be verified on the positioner display or over Bluetooth from a mobile device as explained earlier. As a result of diagnosing and fixing valve issues, loops can be returned to automatic with the same benefits described previously.
Actions that cannot be made directly on the operator console are associated with high stress, workload, and poor health. High levels of stress lead to errors. A good example of this is a manually actuated valve. This was acceptable in the past but not anymore. The recommendation is to upgrade manual valves by adding actuators. As a result of operation from the operator console, workload and stress are reduced.
Inaccurate transmitters make production operators set setpoints with conservative “comfort margins” to not cross limits. Comfort margins cause quality giveaway and high energy consumption. For example, ultrasonic or differential pressure (DP) level transmitters, turbine or PD displacer interface levels, remote seals or temperature sensors direct to system input cards each have their accuracy challenges.
The recommendation is to upgrade these positions with new sensing technology such as non-contacting 80 GHz frequency modulated continuous wave (FMCW) radar for level (Figure 3), magnetic, vortex, or Coriolis flowmeters, electronic remote sensors (ERS) in place of remote seals in most applications, GWR for interface level, and temperature transmitters close to the temperature sensors. For DP flowmeters, upgrade the DP transmitter to a high accuracy and stability model. With more accurate measurements, plants see reduced production cost and greater sustainability.
Custody transfer storage tank level gauges or flowmeters with moving mechanical parts can also be inaccurate. This leads to inventory loss or leaves the customer shorted. For example, servo or float-andtape level gauges and turbine flowmeters are mechanical devices that have accuracy challenges. The recommendation is to upgrade storage tanks with custody transfer certified FMCW radar level gauges with no moving parts. For metering skids, the recommendation is to upgrade from turbine flowmeters to custody transfer certified ultrasonic or Coriolis flowmeters without moving parts. With more accurate measurements, plants avoid inventory losses and avoid shorting customers. Terminals have the confidence to fully use tank capacity.
Package units and skids connected to the main distributed control system (DCS) through hardwiring or RS-485 networking carry limited information, like a single common alarm, to the production operators. Those operators then are forced to send someone out to the module for closer inspection when an alarm occurs. This causes operator stress, potential mistakes, slower problem resolution, and production downtime.
The recommendation is to upgrade the package unit controllers and DCS to use Ethernet, OPC-UA, and Module Type Package (MTP) integration technology (Figure 1). With the complete set of information from the package unit, plants reduce operator stress and production downtime.
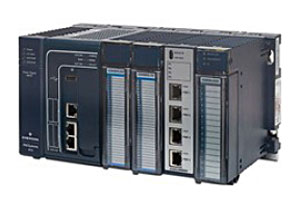
DCS that use proprietary software “connectors” require customcoded application programming interfaces (APIs) for integration of data into apps, which is very costly. Consequently, helpful apps like advanced control, state-based control (procedural automation), and loop tuning do not get adopted in the plant. So, production operators must make various manual interventions that could otherwise be automated with software. This is contributing to operator stress, possibly mistakes, off-spec product, high energy consumption, and low throughput. The recommendation is to upgrade the DCS to use OPC-UA. The added software enables plants to reduce operator stress and off-spec product, increase sustainability, and achieve greater throughput.
Pressure switches only have an on-off contact output, so there is no telling if pressure is ever close to the limit or how fast it is changing. Production operators get no early warning (no prediction). In addition, there is no self-diagnostics so production operators cannot tell if it has failed. This in turn leads to operator stress. When in doubt, production operators must request a manual check on signal validity. The recommendation is to upgrade these positions to pressure transmitters with self-diagnostics flagged as 20 mA. For example, American Petroleum Institute (API) standard 682 recommends transmitters instead of switches for mechanical seals.
Similarly, proximity switches are sometimes used for position feedback, but they only tell you if the valve is fully opened or closed, and there are no self-diagnostics so production operators cannot tell if a switch has failed. This in turn leads to operator stress. When in doubt, production operators must request a manual check on signal validity. The recommendation is to upgrade these valves to position transmitters. With more information, plants can reduce operator stress and increase safety
Mechanical controllers, as found on some control valves in some corners of most plants, are isolated because they are not integrated with the operator consoles. Production operators must go to the field to manually check the pressure or change the setpoint. This leads to operator stress. The recommendation is to upgrade these valves to electronic controllers with networking, enabling remote setpoint and process monitoring from a central location. This helps plants reduce operator stress.