Extend the Reach of Robots with Guide Wheel Based Robot Transfer Units (RTUS)
Flexible automation has exponentially exploded in recent years to the point where robots and cobots are a ubiquitous element of nearly every production environment. The use of robots has expanded well beyond traditional applications in material handling, manufacturing production, machine tending, welding, assembly and product inspection to break into other industries like food service where robots are employed to prepare coffee, pour a glass of beer, and even flip hamburgers on a grill while cooking French fries. Many robot models from numerous manufacturers are available in a variety of formats and range from micro tabletop collaborative robots all the way up to heavy capacity and long reach material transfer equipment capable of manipulating a full-size automobile.
In most installations, the robot is rigidly mounted at a fixed location either on a machine or fastened to the factory floor where work can be completed within the robots’ reach and load capacity. Automation requiring the transfer of materials over long distances or doing work at various locations often involves the very costly addition of more robots. However, the recent addition of Robot Transfer Units as a readymade automation component expands the productive reach of a single robot so that it can complete work anywhere along a track system at a total cost that is often lower than the cost of adding a second robot. See Figure 1.
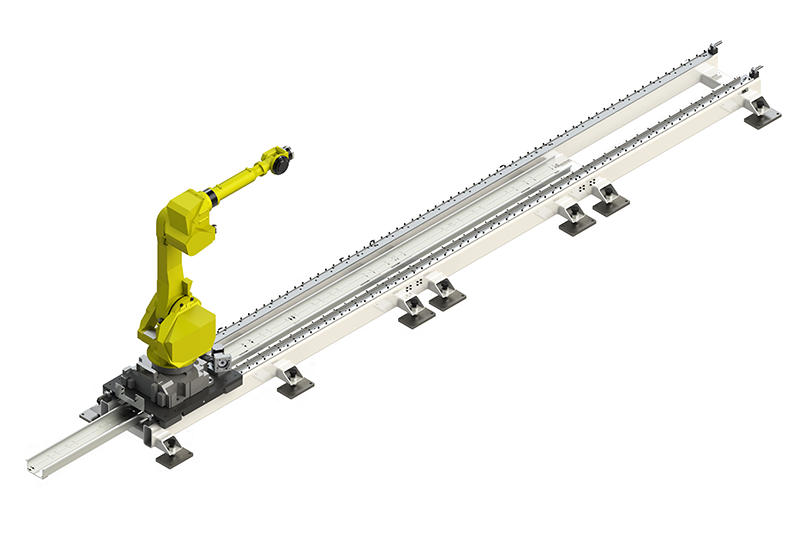
Benefits of utilizing a robot transfer unit
There are many benefits to having a track mounted robot installation. Attaching a robot to the moveable carriage of a transfer unit significantly expands the working envelope or reach of the robot because it can dynamically move down a long track system. Having a larger envelope allows for automated work to occur on very large workpieces such as fairings, aerostructures, or turbine blades. Material handling work can be expanded over a larger area with a single robot transferring products to a variety of production lines or to several machines. A track mounted robot can transfer production between several operations in a work cell instead of being imprisoned at a single workstation. Point-to-point transfer can occur over greater distances and offers added flexibility as is the case with an RTU stacking a variety of packaged products onto multiple different pallets.
Robot arms contain motorized joints that typically provide 6-degrees precision motion. The robot controller calculates the necessary kinematics to move the joints so that the end effector follows a defined path or moves to various programmed points while ensuring that the robot doesn’t crash into itself. Some robot controllers are pre-equipped with a 7th motor drive for controlling a 7th axis of motion. These solutions are a perfect match for utilizing a robot transfer unit because motion can be programmed with the built-in software kinematics. Other installations may require the electronic integration of the RTU drive and motor controls into the overall motion system. The addition of a 7th axis can allow for a fully dynamic robot transfer unit where the track system is manipulated within the kinematics model so that complex profiling becomes possible. Other more simple 7th axis programs provide point-to-point motion for the robot where it can be repositioned to a new location along the RTU track system.
Unique properties of guide wheel based RTU
7th axis robot transfer units from Linear Guide Wheels and tracks as guiding bearings. The guide wheel bearings feature double 90-degree vee angles and are designed to roll on matching 90-degree vee linear track surfaces. See Figure 2. The resulting motion is very low friction and smooth motion over long travel distances. The vee-to-vee geometry of the guide wheel meshed to the linear track creates a self-cleaning wiping action when rolling that will eject debris, ensuring proper function even in dirty factory environments or where process contamination is present.
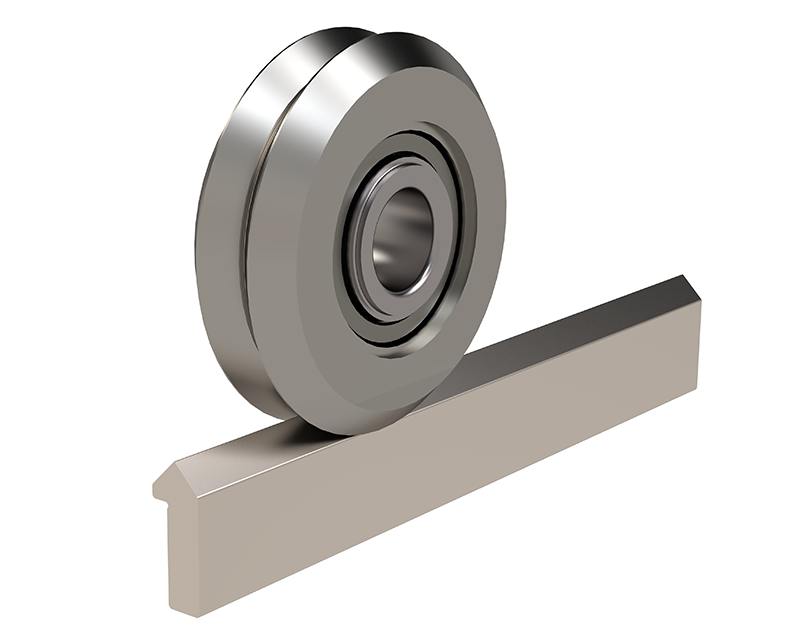
The guide wheels provide industrial grade performance with very limited maintenance that results in a low total cost of ownership. The linear guides only require re-lubrication with light oil and occasional readjustment of the eccentric bearing mounts for consistent wheel-to-track interface engagement. If any wear develops, the eccentric bearings can be adjusted to take out play. The overall design is serviceable with all linear guide components attached with fasteners for rapid removal and replacement using simple hand tools. As a standard offering, the guide wheels and linear track components can be replaced when needed.
Advantage of predesigned solutions
RTU are predesigned automation solutions that can be rapidly integrated into a complete 7th axis configuration. Standardized options, travel lengths, and accessories make selecting and ordering simple and provides expert application engineering assistance with every motion control project.
The complete mechatronics solution that’s ready for robot mounting upon delivery can be sourced from a single supplier while maintaining a consistent support team to ensure long-lasting reliability. As a standard predesigned system, service parts and components are available along with product support into the future.
Guide wheel based RTU systems utilizing groove linear guide wheels and tracks are an engineered solution with known and published performance characteristics. Each RTU has a verified load and thrust capacity so that any of the preselected robot models can be quickly attached, and alternate robot models can be quickly sized and confirmed for use. When the application loads are known, a wheel bearing life estimate can be calculated and service life estimated. With a life estimate, maintenance intervals and maintenance costs can be calculated so that all financial considerations can be evaluated ahead of capital investment.
Longer and more flexible automation
Robot Transfer Units (RTU’s) greatly expand the working envelope of cobots and robots by allowing them to travel down the length of a linear track system. A single RTU mounted robot can perform the work of several robots and can have a lower overall cost. Guide wheel-based motion systems are an ideal choice for long and smooth motion while providing excellent performance in dirty and debris laden operating environments. 7th axis robot transfer units can be programmed to operate in point-to-point or fully dynamic applications where extended robotic reach is needed. RTU with belt drive is suitable for light and medium capacity cobots and cobots and can be mounted in an overhead inverted position to further free up the working envelope.
RTU with gear rack and pinion drive can translate heavy capacity robots at reasonable speed over long distance with a modular tubular steel track design that can be extended after installation. The service life of guide wheel-based robot transfer units can be estimated by calculation because the performance characteristics are known. Expert application engineering support accompanies all Bishop-Wisecarver® RTU systems to ensure the maximum benefit is realized. Extend the reach of robotic applications by dynamically moving a robot down a predesigned track system.